How to Successfully Navigate the Case Interview
How to Successfully Navigate the Case Interview
Interviews are always nerve racking. With a strong desire to put your best foot forward, you can end up putting your foot in your mouth instead. Everyone has done it at one point or another, walking away thinking “wow, that was bad”.
The case interview, a standard step in the hiring process of any consulting firm, has an added element of stress. Not only is your background and character being scrutinized, but so are your problem identification and solving skills. Remaining focused and being clear to let your problem comprehension and concise analysis shine through can be difficult in this situation.
However, as intimidating as a case interview may seem, there are three simple ways to detach from the stress and instead approach the entire process logically to succeed.
Practice
A case interview is no different than any other interview in that you need to present yourself well. However, it does require a much different approach to preparation. When warming up for a fit or a character interview, you polish up on the basics, rehearse responses to standard questions like “why do you want to work here” or “tell me a time you failed and how did you respond”, and generally prepare to speak to content you are well versed in. But in case studies, you don’t know in advance what content you’ll be asked to cover.
So, the first step to preparing for a case interview is to polish your responsive analytical and problem-solving skills by taking advantage of the myriad sample case studies available online. Practice how to separate the stimulus from the question, how to break down the problem, how to identify what information is missing, and how it should be gathered and synthesized.
Do Your Research
Your next step will be to research the company’s terminology.
Study their website and their LinkedIn page, and read any publications you can find in order to learn what their “language” is. A quick perusal of Trindent’s website and LinkedIn page, for example, will show a treasure trove of vocabulary and expressions that make up the standard language we use every day.
Remember to Adapt
During the interview, knowing the company’s nomenclature will help you understand the case, read your interviewer’s queues, structure your responses to fit the company mold, be concise in your answers, and hit the right points rather than explaining around them.
It will also allow you to adapt your style to match that of the interviewer. It may seem like a small thing, but the case will be presented using the company’s language, so pivoting to using their terminology will not only help you understand it better, but will also allow your interviewer to easily follow your thought process as you talk through the solution – all of which will translate into higher scores.
Being well prepared for a case interview takes a lot of time, but it also takes a great deal of stress out of it and sets you up to succeed in the next steps of your consulting career.
Interested in becoming part of our team? Check out our current openings page to find a role that best suits you.
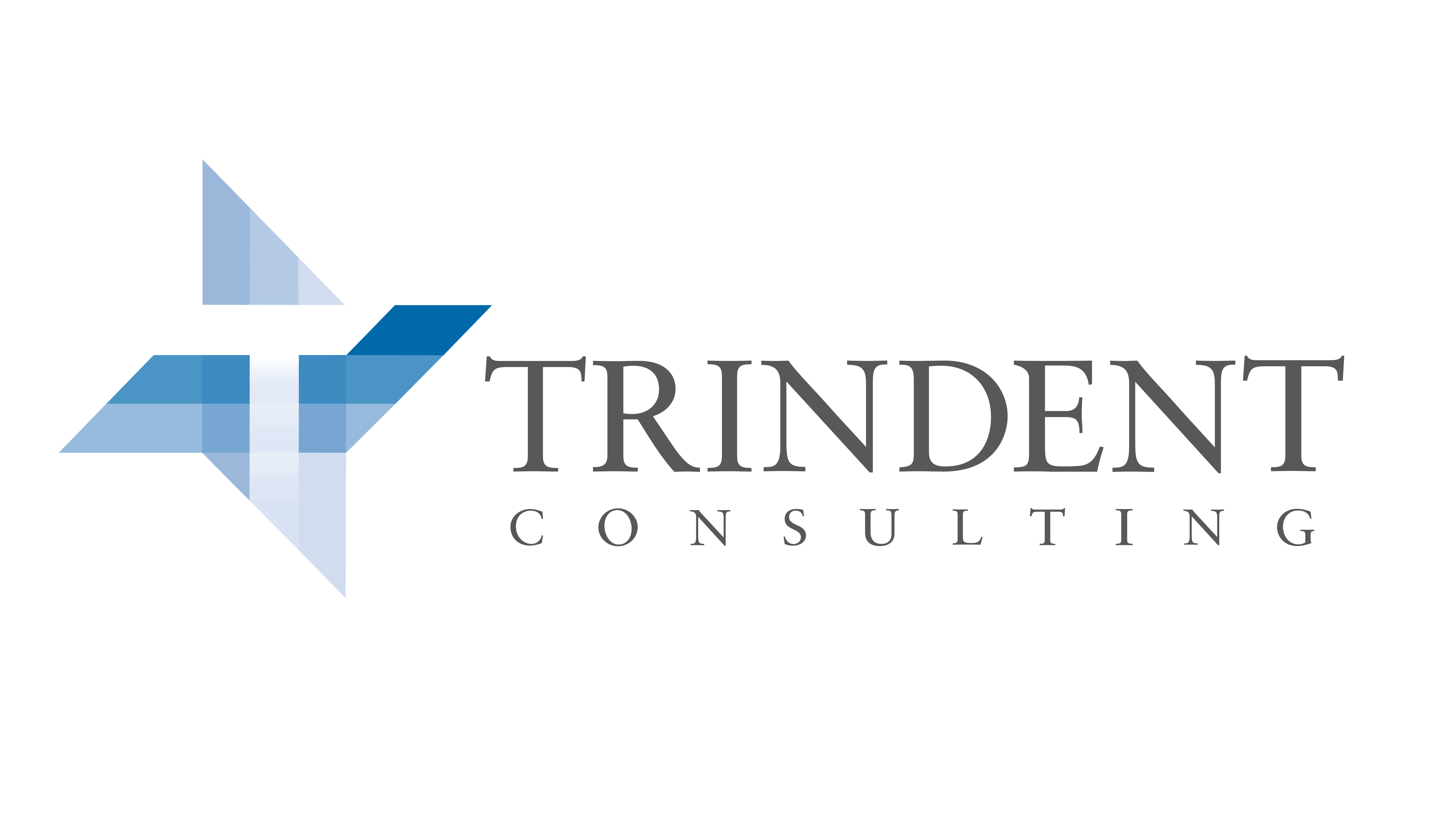
At Trindent Consulting, we are a global technical augmentation company with a passion for solving complex problems in the energy, healthcare, and finance sectors. With over 100 client partnerships, our success centers on prioritizing sustainable profit margin improvements and delivering impactful results.
As a medium-sized firm, we cultivate a close-knit environment where every team member knows one another. Our people are fun, and our work is intriguing and diverse. We actively strive to create an inclusive environment where everyone has equal opportunities for growth and success.
Interested in becoming part of our team? Check out our current openings page to find a role that best suits you.
Interested in topics related to “Building a Career in Consulting”? Click the buttons below to check out our related insights.
Setting Up for Success: A Beginner’s Guide to Consulting
What exactly do consultants do? This is a question commonly asked of consultants by friends, family, or during coffee chats. The truth is, ‘Consultant’ is a broad term covering a wide range of definitions.
In this article, we’ve condensed the essential skills and benefits common to Trindent Consultants. These are the core ingredients that define the consulting lifestyle, enable us to deliver bottom-line results and represent what you can expect from a career in consulting.
C – Change
In consulting, there are two layers of change that are important to master: (1) the ability to accept change; and (2) the ability to instill change. As a consultant, you need to be able to adapt to changing work conditions and environments. By learning to embrace change and expect the unexpected, you will set yourself up for success. Additionally, as a consultant, you are responsible for influencing the client to trust the solutions you are providing. It is imperative that you can deliver on your promises and establish rapport to implement sustainable changes.
O – Organization
You will work with large amounts of information and data throughout the majority of the engagements you are a part of. You may also work on several concurrent engagements with competing deadlines and priorities. By staying organized, productive, and managing your time, you will be able to complete deliverables with a systematic and efficient approach.
N – Network
You will work with incredibly smart people within your consulting firm as well as on your clients’ teams. This will allow you to build professional relationships with ambitious and talented individuals who you can continue to learn from throughout your career.
S – Solutions Oriented
Successful consultants are solutions-oriented – you enjoy the challenge of solving difficult business problems while uncovering effective and innovative solutions.
U – Urgency
One of Trindent’s core values is Perfection with Urgency. As a consultant, you may have new deliverables pop up with tight turnaround times. It is essential to produce a high-quality deliverable efficiently and effectively to ensure it is client-ready within deadlines.
L – Learning
As a consultant, you are going to work on various projects, with a variety of clients in a wide range of industries so you will certainly not be deprived of opportunities to learn! If you are a curious individual with a love of learning, consulting could be the perfect fit.
T – Travel
One of the most exciting parts of consulting is the opportunity to travel. Trindent’s global client base will allow you to fly frequently, live in hotels, and explore new cities, all while bonding with your engagement team.
I – Initiative
As a consultant, you may be expected to lead your own workstream during an engagement. You should be comfortable stepping up to the challenge and act with little to no supervision.
N – Navigate Ambiguous Situations
At times, you will face challenging and ambiguous business problems. These situations will push you to be comfortable with the unknown and uncover insights from complex problems.
G – Growth
Aligned to the love of learning, working in consulting will expedite your professional growth immensely. Being exposed to a variety of clients, industries, and business practices will allow you to gain unparalleled experience and knowledge within a short timeframe.
Above all, Consultants Make It Happen™. We develop insights, instill change, and deliver sustainable results for our clients. By honing the skills mentioned and demonstrating them during your work or throughout the interview process, you will be setting yourself up for a successful career.
Top Reads to Break into Consulting and Succeed
Unlike careers in medicine, law or priesthood, one doesn’t require seven, eight or ten years of education to break into consulting. However, it might often seem that way. Statistically, more and more top business school grads are gravitating towards a career in Management Consulting, so competition has never been tougher. Listed below, are some books that can greatly assist you, not only in breaking into consulting but also in succeeding once you’re there.
-
The McKinsey Way – Ethan M. Rasiel
Quick Glance: The McKinsey Way gives you a quick glimpse into the life of a McKinsey Consultant. The book discussed in simple terms how to run a meeting, how to sell yourself, your business and your ideas, and how to train yourself to think like a consultant.
Why Read? Ethan’s deep dive into the McKinsey way lessens the learning curve associated with many consultancies.
-
Case Interview Secrets – Victor Cheng
Quick Glance: Considered to be the bible for preparing for case interviews. Whether you are brand new to the process or a seasoned vet, this book is the gold standard in giving you the tools to better structure your thoughts, apply logic throughout a case and present and synthesize ideas effectively and coherently.
Why Read? Case Interview Secrets walks you through each stage in the case interview process and the examples at the back are good primers to the real thing.
-
Smarter, Faster, Better – Charles Duhigg
Quick Glance: In this book, Charles Duhigg uses captivating real-world examples to convey ideas on how to improve yourself, your way of thinking and even your business.
Why Read? A big part of consulting is being able to convey ideas to clients using anecdotes and stories to be more relatable and effective.
-
HBR’s 10 Must Reads: The Essentials
Quick Glance: The Essentials are precisely that – the basic requirements of business knowledge that you need to understand how businesses operate in their respective ecosystems.
Why Read? You are often expected to learn quickly when placed on a new study or engagement. Having a working business knowledge can provide the necessary context to help make sense of things.
Interested in learning more career tips? Follow us on LinkedIn for the latest news!
Refinery Maintenance: The Work Management Process
Refinery Maintenance: The Work Management Process
In any equipment intensive sector, there is almost never a quiet day – and a refinery is no exception. Even the best-planned days can be full of interruptions – failures and other unplanned events that disrupt the schedule and cause system slowdowns or outages.
But a well-curated and properly executed Work Management Process can smooth the impact of these disruptions and enable good Risk Based Decision Making so that refineries can reduce the costs associated with equipment failures, inefficient work execution, process interruptions, overtime, and rushed orders.
Typical Work Management Process
During the first part of the process – Work Need Identification – enhanced training can increase operator understanding of the processes and equipment, while empowering them to better identify failures before they occur. Properly designed and executed Preventative Maintenance for each piece of equipment can enable better identification of failing equipment and increase the equipment’s longevity.
Once a failure is identified, the Operator generates a work notification in the refinery’s Computerized Maintenance Management System (CMMS)or Enterprise Asset Management (EAM) software. Often, these systems are not optimally set-up to enable proper data collection, so it’s important that operators receive proper training in order to ensure that work notifications are of sufficient quality and detail with reduced operator variation.
After the notification is submitted to and approved by a supervisor, a Planner determines which craftspeople and tools are required to fix the failure and how long the work will take to complete. An inaccurate plan can lead to inefficient Work Order Execution as the proper craftspeople may not be involved, the proper tools may not be available, or the schedule may be inaccurate in terms of its duration. Improving the planning process using accurate data can prevent these deficiencies.
Work Order Scheduling is often a challenging area, as there is a limited amount of both human and financial resources, but a long list of work that needs to be completed. These scheduling meetings are typically the embodiment of “the squeaky wheel gets the grease”, with the loudest individuals in the room receiving the most resources. As a result, Preventative Maintenance efforts tend to be neglected, and this myopic view creates a slippery slope of increased equipment failures in the long-term. Creating Standard Operating Procedures and Work Management Risk Matrices can support work prioritization and strike the balance between preventative and reactive work orders. The same logic can be used to prioritize and decrease the Maintenance Backlog. It’s important to note here that the proper criteria should be used in work prioritization to reach desired outcomes; frequently, refineries use incorrect criteria, which reduces the effectiveness of prioritization efforts.
Work Order Close-out is one of the most important steps in the process but is often neglected or improperly completed. A proper Work Order Close-out results in better data collection and more informed decision making. This information can be used in a continuous improvement process that allows Planners to fine-tune Work Order Planning. Additionally, failure code data can be used to identify root causes of failures and support Defect Elimination programs.
Interested in topics related to “Refinery Maintenance”? Click the buttons below to check out our related industry insights.
Vital Role of Tank Gauging in Refineries: Ensuring Accuracy and Safety
Refineries play a critical role in the processing of crude oil and the production of various petroleum products. Within these complex facilities, the storage and management of liquids, such as crude oil, intermediates, and finished products are of utmost importance. To ensure efficient operations, accurate inventory management, and safe working conditions, refineries rely heavily on tank gauging systems. The following will explore the significance of tank gauging in refineries and how it contributes to the overall success of these facilities.
Different Tank Gauging Methods
While different gauging techniques are used depending on the type of tank and the unique properties of the liquid being stored, tank gauging methods can be divided into two general categories – manual and automatic. An automatic tank gauge (ATG) is an electronic device whose purpose is to continuously monitor levels. ATGs also provide refinery operators with details regarding what is happening inside the tank (e.g., changes in level, level warnings, water level and volume, and temperature). Alternatively, a manual gauge can be carried out using one of 2 techniques: innage (tells you the actual depth of the liquid inside the tank) or outage (measures the part of the tank that is not filled with liquid).
While it can be tempting to solely rely on ATGs for information, recall that all equipment must be calibrated to ensure accuracy. Considering the size of storage tanks, a difference of a quarter inch in level measurement could equal thousands of barrels. Now that we have a better understanding of different methods for tank gauging, let’s explore some of the benefits of using a combined approach for ATG and manual tank gauging at the refinery.
Accurate Inventory Management
Tank gauging provides accurate measurement of liquid levels and volumes in storage tanks. Precise knowledge of inventory levels is essential for production planning and scheduling. Accurate inventory data helps optimize storage capacity and minimize product losses. Compliance with Safety Regulations Refineries operate under strict safety regulations and guidelines. Tank gauging ensures compliance with regulations regarding storage tank safety. Accurate level monitoring helps prevent overfilling and the associated risks. Moreover, by eliminating inventory inaccuracy as a potential source for error, the refinery is better able to reconcile mass balance and more efficiently identify sources of loss (e.g., meter equipment issues, density measurements, etc.).
Leak Detection and Environmental Protection
Tank gauging systems play a crucial role in early leak detection. Continuous monitoring of tank levels helps identify potential leaks promptly. Detecting leaks promptly minimizes environmental impact and prevents product loss.
Operational Efficiency
Tank gauging systems enable real-time monitoring of tank levels and product movement. Operators can track inventory levels, identify bottlenecks, and optimize processes. Accurate data helps streamline operations, reduce downtime, and increase efficiency.
Maintenance and Asset Management
Tank gauging systems aid in predictive maintenance and asset management. Continuous monitoring of tank conditions helps identify maintenance needs. Early detection of equipment malfunctions reduces the risk of costly breakdowns.
Integration with Control Systems
Tank gauging systems can be integrated with refinery control systems. Integration allows for seamless monitoring and control of tank levels and operations. Real-time data integration facilitates decision-making and enhances overall refinery control.
Emergency Response and Contingency Planning
In the event of emergencies, such as fires or leaks, tank gauging data is invaluable. Accurate and up-to-date information aids emergency response teams. Tank gauging systems assist in developing effective contingency plans.
Calibration and Accuracy Verification
Regular calibration and verification of tank gauging systems are essential. Calibration ensures accurate measurement and reliable data. Regular verification confirms that the system remains within acceptable accuracy limits.
Operator Safety and Ease of Operation
Tank gauging systems enhance operator safety and ease of operation. Accurate level measurements reduce the need for manual gauging, minimizing exposure to hazards. Automated systems provide operators with real-time information, enhancing situational awareness.
Continuous Improvement and Optimization
In conclusion, refineries are constantly striving for improvement and optimization. Tank gauging data plays a vital role in identifying opportunities for optimization. Analyzing historical data helps refine processes, reduce waste, and enhance overall performance. Tank gauging is an indispensable component of refinery operations. It ensures accurate inventory management, compliance with safety regulations, early leak detection, operational efficiency, and much more. By investing in reliable tank gauging systems and embracing continuous improvement, refineries can achieve optimal performance, maintain safety standards, and contribute to the sustainable growth of the industry.
This article was written by Francesca D’Urso, an Engagement Manager at Trindent Consulting.
Refinery Maintenance: Planning for Success
As processors and storage become cheaper and more efficient, more and more companies want to analyze increasing amounts of data and use artificial intelligence to support Risk Based Decision Making; and refineries are no different.
Predictive Maintenance offers refineries an opportunity to determine the current condition of equipment to predict when a failure will occur. This gives refineries a potential to reduce Operating Expenses by performing preventative maintenance only when it is warranted and by reducing the costs associated with Reactive Maintenance. Predictive Maintenance programs are high CAPEX and, unfortunately, most refineries do not have adequate processes and quality data available to make this transition worthwhile. Trindent provides refineries with low to no CAPEX solutions that build the fundamentals required to make the first step towards Predictive Maintenance.
Foundations for Success
Before a refinery can implement a holistic Predictive Maintenance program, they first need to establish a pilot program. Creating the right foundation allows the refinery to plan for success and implement a program using data-driven decision making to determine where the initiative will have the most impact. Proper foundations also allow for improved refinery operations and a reduction in Operating Expenses in the interim.
- Proper Preventative Maintenance: Preventative maintenance reduces the likelihood of equipment failure by performing routine checks or interventions on the equipment. A proper maintenance program will occur frequently enough to detect failures but not be unnecessarily burdensome to maintenance personnel. As part of this, it’s important to understand correct Preventative Maintenance tasks, durations, and crafts people allow for refinery management to focus predictive maintenance efforts on the equipment that cost the most to maintain. Without proper Preventative Maintenance tasks in place, there will be inadequate follow-up action from predictive maintenance findings.
- Data Quality: During the work management process there are many opportunities to collect the right data; however, refineries often lack the processes and training to collect data that is sufficiently detailed. Improving maintenance programs for instruments and sensors allows the refinery to identify whether the quality of the data is adequate or if the right sensors are even in place. Better data quality allows for management to focus predictive maintenance efforts on specific failures that result in process interruptions. Furthermore, the use of Defect Elimination programs can give the refinery insights into the conditions that cause failure, allowing for a more effective predictive maintenance program.
- Culture: Without building a proactive culture, a predictive maintenance program is destined to be an expensive, but short-lived endeavor. Establishing the right training, tools, dashboards, and communication methodologies allows for results to be sustained. Once the refinery has shifted from a reactive to a proactive culture then the predictive maintenance program can be successful.
At Trindent, we focus on tangible results and showing improvement through data. This data-driven approach links our results to financial or other key performance indicators. In addition, we make sustainability a key part of each engagement, and train your employees to sustain results.
Refinery Maintenance: Planning for Success
Refinery Maintenance: Planning for Success
As processors and storage become cheaper and more efficient, more and more companies want to analyze increasing amounts of data and use artificial intelligence to support Risk Based Decision Making; and refineries are no different.
Predictive Maintenance offers refineries an opportunity to determine the current condition of equipment to predict when a failure will occur. This gives refineries a potential to reduce Operating Expenses by performing preventative maintenance only when it is warranted and by reducing the costs associated with Reactive Maintenance. Predictive Maintenance programs are high CAPEX and, unfortunately, most refineries do not have adequate processes and quality data available to make this transition worthwhile. Trindent provides refineries with low to no CAPEX solutions that build the fundamentals required to make the first step towards Predictive Maintenance.
Foundations for Success
Before a refinery can implement a holistic Predictive Maintenance program, they first need to establish a pilot program. Creating the right foundation allows the refinery to plan for success and implement a program using data-driven decision making to determine where the initiative will have the most impact. Proper foundations also allow for improved refinery operations and a reduction in Operating Expenses in the interim.
- Proper Preventative Maintenance: Preventative maintenance reduces the likelihood of equipment failure by performing routine checks or interventions on the equipment. A proper maintenance program will occur frequently enough to detect failures but not be unnecessarily burdensome to maintenance personnel. As part of this, it’s important to understand correct Preventative Maintenance tasks, durations, and crafts people allow for refinery management to focus predictive maintenance efforts on the equipment that cost the most to maintain. Without proper Preventative Maintenance tasks in place, there will be inadequate follow-up action from predictive maintenance findings.
- Data Quality: During the work management process there are many opportunities to collect the right data; however, refineries often lack the processes and training to collect data that is sufficiently detailed. Improving maintenance programs for instruments and sensors allows the refinery to identify whether the quality of the data is adequate or if the right sensors are even in place. Better data quality allows for management to focus predictive maintenance efforts on specific failures that result in process interruptions. Furthermore, the use of Defect Elimination programs can give the refinery insights into the conditions that cause failure, allowing for a more effective predictive maintenance program.
- Culture: Without building a proactive culture, a predictive maintenance program is destined to be an expensive, but short-lived endeavor. Establishing the right training, tools, dashboards, and communication methodologies allows for results to be sustained. Once the refinery has shifted from a reactive to a proactive culture then the predictive maintenance program can be successful.
At Trindent, we focus on tangible results and showing improvement through data. This data-driven approach links our results to financial or other key performance indicators. In addition, we make sustainability a key part of each engagement, and train your employees to sustain results.
Interested in topics related to “Refinery Maintenance”? Click the buttons below to check out our related industry insights.
Vital Role of Tank Gauging in Refineries: Ensuring Accuracy and Safety
Refineries play a critical role in the processing of crude oil and the production of various petroleum products. Within these complex facilities, the storage and management of liquids, such as crude oil, intermediates, and finished products are of utmost importance. To ensure efficient operations, accurate inventory management, and safe working conditions, refineries rely heavily on tank gauging systems. The following will explore the significance of tank gauging in refineries and how it contributes to the overall success of these facilities.
Different Tank Gauging Methods
While different gauging techniques are used depending on the type of tank and the unique properties of the liquid being stored, tank gauging methods can be divided into two general categories – manual and automatic. An automatic tank gauge (ATG) is an electronic device whose purpose is to continuously monitor levels. ATGs also provide refinery operators with details regarding what is happening inside the tank (e.g., changes in level, level warnings, water level and volume, and temperature). Alternatively, a manual gauge can be carried out using one of 2 techniques: innage (tells you the actual depth of the liquid inside the tank) or outage (measures the part of the tank that is not filled with liquid).
While it can be tempting to solely rely on ATGs for information, recall that all equipment must be calibrated to ensure accuracy. Considering the size of storage tanks, a difference of a quarter inch in level measurement could equal thousands of barrels. Now that we have a better understanding of different methods for tank gauging, let’s explore some of the benefits of using a combined approach for ATG and manual tank gauging at the refinery.
Accurate Inventory Management
Tank gauging provides accurate measurement of liquid levels and volumes in storage tanks. Precise knowledge of inventory levels is essential for production planning and scheduling. Accurate inventory data helps optimize storage capacity and minimize product losses. Compliance with Safety Regulations Refineries operate under strict safety regulations and guidelines. Tank gauging ensures compliance with regulations regarding storage tank safety. Accurate level monitoring helps prevent overfilling and the associated risks. Moreover, by eliminating inventory inaccuracy as a potential source for error, the refinery is better able to reconcile mass balance and more efficiently identify sources of loss (e.g., meter equipment issues, density measurements, etc.).
Leak Detection and Environmental Protection
Tank gauging systems play a crucial role in early leak detection. Continuous monitoring of tank levels helps identify potential leaks promptly. Detecting leaks promptly minimizes environmental impact and prevents product loss.
Operational Efficiency
Tank gauging systems enable real-time monitoring of tank levels and product movement. Operators can track inventory levels, identify bottlenecks, and optimize processes. Accurate data helps streamline operations, reduce downtime, and increase efficiency.
Maintenance and Asset Management
Tank gauging systems aid in predictive maintenance and asset management. Continuous monitoring of tank conditions helps identify maintenance needs. Early detection of equipment malfunctions reduces the risk of costly breakdowns.
Integration with Control Systems
Tank gauging systems can be integrated with refinery control systems. Integration allows for seamless monitoring and control of tank levels and operations. Real-time data integration facilitates decision-making and enhances overall refinery control.
Emergency Response and Contingency Planning
In the event of emergencies, such as fires or leaks, tank gauging data is invaluable. Accurate and up-to-date information aids emergency response teams. Tank gauging systems assist in developing effective contingency plans.
Calibration and Accuracy Verification
Regular calibration and verification of tank gauging systems are essential. Calibration ensures accurate measurement and reliable data. Regular verification confirms that the system remains within acceptable accuracy limits.
Operator Safety and Ease of Operation
Tank gauging systems enhance operator safety and ease of operation. Accurate level measurements reduce the need for manual gauging, minimizing exposure to hazards. Automated systems provide operators with real-time information, enhancing situational awareness.
Continuous Improvement and Optimization
In conclusion, refineries are constantly striving for improvement and optimization. Tank gauging data plays a vital role in identifying opportunities for optimization. Analyzing historical data helps refine processes, reduce waste, and enhance overall performance. Tank gauging is an indispensable component of refinery operations. It ensures accurate inventory management, compliance with safety regulations, early leak detection, operational efficiency, and much more. By investing in reliable tank gauging systems and embracing continuous improvement, refineries can achieve optimal performance, maintain safety standards, and contribute to the sustainable growth of the industry.
This article was written by Francesca D’Urso, an Engagement Manager at Trindent Consulting.
Refinery Maintenance: The Work Management Process
In any equipment intensive sector, there is almost never a quiet day – and a refinery is no exception. Even the best-planned days can be full of interruptions – failures and other unplanned events that disrupt the schedule and cause system slowdowns or outages.
But a well-curated and properly executed Work Management Process can smooth the impact of these disruptions and enable good Risk Based Decision Making so that refineries can reduce the costs associated with equipment failures, inefficient work execution, process interruptions, overtime, and rushed orders.
Typical Work Management Process
During the first part of the process – Work Need Identification – enhanced training can increase operator understanding of the processes and equipment, while empowering them to better identify failures before they occur. Properly designed and executed Preventative Maintenance for each piece of equipment can enable better identification of failing equipment and increase the equipment’s longevity.
Once a failure is identified, the Operator generates a work notification in the refinery’s Computerized Maintenance Management System (CMMS)or Enterprise Asset Management (EAM) software. Often, these systems are not optimally set-up to enable proper data collection, so it’s important that operators receive proper training in order to ensure that work notifications are of sufficient quality and detail with reduced operator variation.
After the notification is submitted to and approved by a supervisor, a Planner determines which craftspeople and tools are required to fix the failure and how long the work will take to complete. An inaccurate plan can lead to inefficient Work Order Execution as the proper craftspeople may not be involved, the proper tools may not be available, or the schedule may be inaccurate in terms of its duration. Improving the planning process using accurate data can prevent these deficiencies.
Work Order Scheduling is often a challenging area, as there is a limited amount of both human and financial resources, but a long list of work that needs to be completed. These scheduling meetings are typically the embodiment of “the squeaky wheel gets the grease”, with the loudest individuals in the room receiving the most resources. As a result, Preventative Maintenance efforts tend to be neglected, and this myopic view creates a slippery slope of increased equipment failures in the long-term. Creating Standard Operating Procedures and Work Management Risk Matrices can support work prioritization and strike the balance between preventative and reactive work orders. The same logic can be used to prioritize and decrease the Maintenance Backlog. It’s important to note here that the proper criteria should be used in work prioritization to reach desired outcomes; frequently, refineries use incorrect criteria, which reduces the effectiveness of prioritization efforts.
Work Order Close-out is one of the most important steps in the process but is often neglected or improperly completed. A proper Work Order Close-out results in better data collection and more informed decision making. This information can be used in a continuous improvement process that allows Planners to fine-tune Work Order Planning. Additionally, failure code data can be used to identify root causes of failures and support Defect Elimination programs.
Vital Role of Tank Gauging in Refineries: Ensuring Accuracy and Safety
Vital Role of Tank Gauging in Refineries: Ensuring Accuracy and Safety
Refineries play a critical role in the processing of crude oil and the production of various petroleum products. Within these complex facilities, the storage and management of liquids, such as crude oil, intermediates, and finished products are of utmost importance. To ensure efficient operations, accurate inventory management, and safe working conditions, refineries rely heavily on tank gauging systems. The following will explore the significance of tank gauging in refineries and how it contributes to the overall success of these facilities.
Different Tank Gauging Methods
While different gauging techniques are used depending on the type of tank and the unique properties of the liquid being stored, tank gauging methods can be divided into two general categories – manual and automatic. An automatic tank gauge (ATG) is an electronic device whose purpose is to continuously monitor levels. ATGs also provide refinery operators with details regarding what is happening inside the tank (e.g., changes in level, level warnings, water level and volume, and temperature). Alternatively, a manual gauge can be carried out using one of 2 techniques: innage (tells you the actual depth of the liquid inside the tank) or outage (measures the part of the tank that is not filled with liquid).
While it can be tempting to solely rely on ATGs for information, recall that all equipment must be calibrated to ensure accuracy. Considering the size of storage tanks, a difference of a quarter inch in level measurement could equal thousands of barrels. Now that we have a better understanding of different methods for tank gauging, let’s explore some of the benefits of using a combined approach for ATG and manual tank gauging at the refinery.
Accurate Inventory Management
Tank gauging provides accurate measurement of liquid levels and volumes in storage tanks. Precise knowledge of inventory levels is essential for production planning and scheduling. Accurate inventory data helps optimize storage capacity and minimize product losses. Compliance with Safety Regulations Refineries operate under strict safety regulations and guidelines. Tank gauging ensures compliance with regulations regarding storage tank safety. Accurate level monitoring helps prevent overfilling and the associated risks. Moreover, by eliminating inventory inaccuracy as a potential source for error, the refinery is better able to reconcile mass balance and more efficiently identify sources of loss (e.g., meter equipment issues, density measurements, etc.).
Leak Detection and Environmental Protection
Tank gauging systems play a crucial role in early leak detection. Continuous monitoring of tank levels helps identify potential leaks promptly. Detecting leaks promptly minimizes environmental impact and prevents product loss.
Operational Efficiency
Tank gauging systems enable real-time monitoring of tank levels and product movement. Operators can track inventory levels, identify bottlenecks, and optimize processes. Accurate data helps streamline operations, reduce downtime, and increase efficiency.
Maintenance and Asset Management
Tank gauging systems aid in predictive maintenance and asset management. Continuous monitoring of tank conditions helps identify maintenance needs. Early detection of equipment malfunctions reduces the risk of costly breakdowns.
Integration with Control Systems
Tank gauging systems can be integrated with refinery control systems. Integration allows for seamless monitoring and control of tank levels and operations. Real-time data integration facilitates decision-making and enhances overall refinery control.
Emergency Response and Contingency Planning
In the event of emergencies, such as fires or leaks, tank gauging data is invaluable. Accurate and up-to-date information aids emergency response teams. Tank gauging systems assist in developing effective contingency plans.
Calibration and Accuracy Verification
Regular calibration and verification of tank gauging systems are essential. Calibration ensures accurate measurement and reliable data. Regular verification confirms that the system remains within acceptable accuracy limits.
Operator Safety and Ease of Operation
Tank gauging systems enhance operator safety and ease of operation. Accurate level measurements reduce the need for manual gauging, minimizing exposure to hazards. Automated systems provide operators with real-time information, enhancing situational awareness.
Continuous Improvement and Optimization
In conclusion, refineries are constantly striving for improvement and optimization. Tank gauging data plays a vital role in identifying opportunities for optimization. Analyzing historical data helps refine processes, reduce waste, and enhance overall performance. Tank gauging is an indispensable component of refinery operations. It ensures accurate inventory management, compliance with safety regulations, early leak detection, operational efficiency, and much more. By investing in reliable tank gauging systems and embracing continuous improvement, refineries can achieve optimal performance, maintain safety standards, and contribute to the sustainable growth of the industry.
This article was written by Francesca D’Urso, an Engagement Manager at Trindent Consulting.
Interested in topics related to “Refinery Maintenance”? Click the buttons below to check out our related industry insights.
Refinery Maintenance: Planning for Success
As processors and storage become cheaper and more efficient, more and more companies want to analyze increasing amounts of data and use artificial intelligence to support Risk Based Decision Making; and refineries are no different.
Predictive Maintenance offers refineries an opportunity to determine the current condition of equipment to predict when a failure will occur. This gives refineries a potential to reduce Operating Expenses by performing preventative maintenance only when it is warranted and by reducing the costs associated with Reactive Maintenance. Predictive Maintenance programs are high CAPEX and, unfortunately, most refineries do not have adequate processes and quality data available to make this transition worthwhile. Trindent provides refineries with low to no CAPEX solutions that build the fundamentals required to make the first step towards Predictive Maintenance.
Foundations for Success
Before a refinery can implement a holistic Predictive Maintenance program, they first need to establish a pilot program. Creating the right foundation allows the refinery to plan for success and implement a program using data-driven decision making to determine where the initiative will have the most impact. Proper foundations also allow for improved refinery operations and a reduction in Operating Expenses in the interim.
- Proper Preventative Maintenance: Preventative maintenance reduces the likelihood of equipment failure by performing routine checks or interventions on the equipment. A proper maintenance program will occur frequently enough to detect failures but not be unnecessarily burdensome to maintenance personnel. As part of this, it’s important to understand correct Preventative Maintenance tasks, durations, and crafts people allow for refinery management to focus predictive maintenance efforts on the equipment that cost the most to maintain. Without proper Preventative Maintenance tasks in place, there will be inadequate follow-up action from predictive maintenance findings.
- Data Quality: During the work management process there are many opportunities to collect the right data; however, refineries often lack the processes and training to collect data that is sufficiently detailed. Improving maintenance programs for instruments and sensors allows the refinery to identify whether the quality of the data is adequate or if the right sensors are even in place. Better data quality allows for management to focus predictive maintenance efforts on specific failures that result in process interruptions. Furthermore, the use of Defect Elimination programs can give the refinery insights into the conditions that cause failure, allowing for a more effective predictive maintenance program.
- Culture: Without building a proactive culture, a predictive maintenance program is destined to be an expensive, but short-lived endeavor. Establishing the right training, tools, dashboards, and communication methodologies allows for results to be sustained. Once the refinery has shifted from a reactive to a proactive culture then the predictive maintenance program can be successful.
At Trindent, we focus on tangible results and showing improvement through data. This data-driven approach links our results to financial or other key performance indicators. In addition, we make sustainability a key part of each engagement, and train your employees to sustain results.
Refinery Maintenance: The Work Management Process
In any equipment intensive sector, there is almost never a quiet day – and a refinery is no exception. Even the best-planned days can be full of interruptions – failures and other unplanned events that disrupt the schedule and cause system slowdowns or outages.
But a well-curated and properly executed Work Management Process can smooth the impact of these disruptions and enable good Risk Based Decision Making so that refineries can reduce the costs associated with equipment failures, inefficient work execution, process interruptions, overtime, and rushed orders.
Typical Work Management Process
During the first part of the process – Work Need Identification – enhanced training can increase operator understanding of the processes and equipment, while empowering them to better identify failures before they occur. Properly designed and executed Preventative Maintenance for each piece of equipment can enable better identification of failing equipment and increase the equipment’s longevity.
Once a failure is identified, the Operator generates a work notification in the refinery’s Computerized Maintenance Management System (CMMS)or Enterprise Asset Management (EAM) software. Often, these systems are not optimally set-up to enable proper data collection, so it’s important that operators receive proper training in order to ensure that work notifications are of sufficient quality and detail with reduced operator variation.
After the notification is submitted to and approved by a supervisor, a Planner determines which craftspeople and tools are required to fix the failure and how long the work will take to complete. An inaccurate plan can lead to inefficient Work Order Execution as the proper craftspeople may not be involved, the proper tools may not be available, or the schedule may be inaccurate in terms of its duration. Improving the planning process using accurate data can prevent these deficiencies.
Work Order Scheduling is often a challenging area, as there is a limited amount of both human and financial resources, but a long list of work that needs to be completed. These scheduling meetings are typically the embodiment of “the squeaky wheel gets the grease”, with the loudest individuals in the room receiving the most resources. As a result, Preventative Maintenance efforts tend to be neglected, and this myopic view creates a slippery slope of increased equipment failures in the long-term. Creating Standard Operating Procedures and Work Management Risk Matrices can support work prioritization and strike the balance between preventative and reactive work orders. The same logic can be used to prioritize and decrease the Maintenance Backlog. It’s important to note here that the proper criteria should be used in work prioritization to reach desired outcomes; frequently, refineries use incorrect criteria, which reduces the effectiveness of prioritization efforts.
Work Order Close-out is one of the most important steps in the process but is often neglected or improperly completed. A proper Work Order Close-out results in better data collection and more informed decision making. This information can be used in a continuous improvement process that allows Planners to fine-tune Work Order Planning. Additionally, failure code data can be used to identify root causes of failures and support Defect Elimination programs.