Trindent Develops Accurate Post-Ethanol T-50 Model That Yields $12M in Savings
Trindent is thrilled to share the exciting news of our successful development of an accurate post-ethanol T50 model, marking a significant achievement that has not only resulted in a remarkable reduction in buffers but has also facilitated a 4% increase in butane blending between November and January 2023, translating to impressive financial benefits totaling $12,000,000.
Developing accurate post-ethanol models presents significant challenges for many refineries, particularly when it comes to predicting T50—a key distillation parameter. Ethanol blending exhibits near-azeotrope behavior that severely affects the shape of the E10 distillation curve, making precise modeling complex and demanding.
Moreover, the difficulty in achieving accurate models is compounded by the inherent noise in the data set, such as ethanol blend volume and accurate E0 D86 measurements, which often hinder the development of reliable models.
Despite these challenges, the Trindent team was able to deliver outstanding results to the client.
An achievement like this highlights the importance of precise modeling and data accuracy in optimizing refinery operations and maximizing profitability.
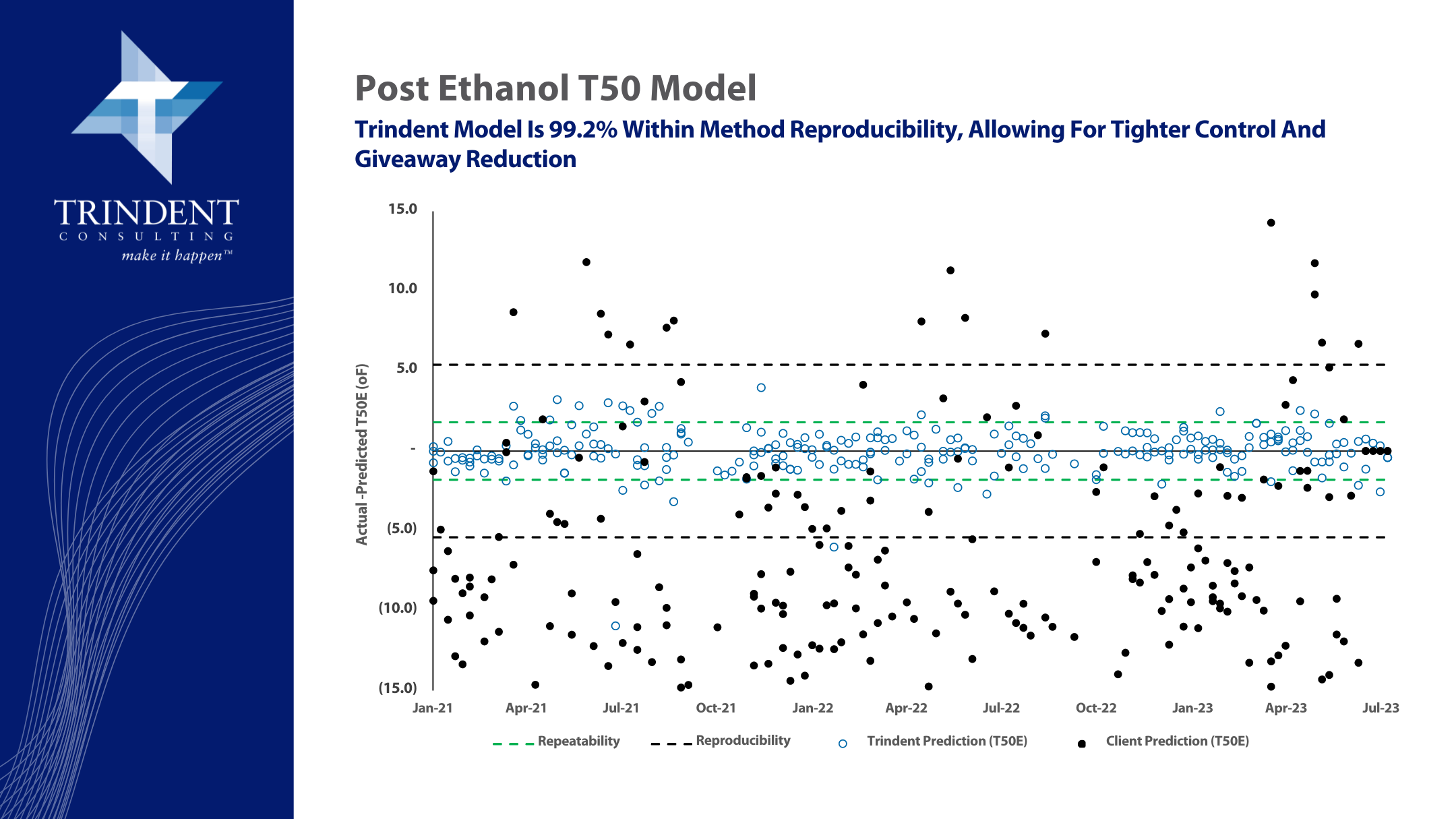
At Trindent Consulting, we’re fueled by a passion for solving the most complex of problems in the energy sector. With expertise in gasoline blending optimization, we help clients achieve significant financial benefits by:
- Developing Accurate Post-Ethanol Models: We develop accurate post-ethanol models, addressing the complexities introduced by ethanol blending and ensuring accurate predictions of key parameters like T50. By leveraging our expertise, refineries can optimize their blending practices and achieve superior fuel quality.
- Reducing Operational Buffers: We understand the importance of maximizing blending efficiency to enhance refinery profitability. We help refineries minimize operational buffers, ensuring optimal utilization of resources and streamlining the blending process for maximum efficiency.
- Enhancing Data Accuracy and Reliability: In an industry where data-driven decision-making is paramount, we excel in enhancing data accuracy and reliability such as ethanol volume %. We empower refineries to make informed decisions with confidence, driving operational excellence and performance improvement without capital investments of software changes of any kind.
- Providing Tailored Solutions for Profitability: Every refinery faces unique challenges, and we recognize the importance of tailored solutions to address specific needs. Our team collaborates with clients to understand their distinct requirements and develop customized strategies aimed at increasing profitability and optimizing refinery processes effectively.
Interested in learning more about our services in the downstream sector? Check out our Energy page to explore our expertise and discover how we drive client success.
Interested in topics related to gasoline blending? Click the buttons below to check out our related industry insights.
“How to Establish a Good Ethanol Uplift Model?”
“How to establish a good ethanol uplift model?” has been a common question when it comes to gasoline blending. With the addition of 10% ethanol to a majority of gasoline products, accurate prediction of the final fuel properties is critical to mitigate margin erosion. With years of experience in blending optimization projects, at Trindent we have developed specific expertise in this area, and here are some insights:
Ethanol Uplift Model Best Practices
Each refinery has its configurations that are developed as a result of the molecules they are making. Therefore, picking the right independent variables to start the development of the model is critical. It starts with understanding the principle of what Octane Number (ON) is, and how this property is related to the chemical molecules inside the gasoline. Typically, a refinery can use as much as 7-8 independent variables, and around 10-15 iterations before finding the perfect model which is not only accurate but also intuitive. The complexity of the model is also important as you want to make it sophisticated enough to provide the accuracy you want, but also simple enough to integrate into the existing system with ease.
Managing Component Distribution
Once a model is developed – the next question would be – how do we optimize it? In addition to adjusting the ON of the neat blend stock (which is often the only approach most refineries take), refineries may take advantage of other property and compositional requirements between to maximize the overall benefit of ON uplift.
Going Beyond ON
While a lot of focus on the ethanol model is about ON, it is imperative to consider other properties that are also affected by ethanol. Therefore, a mature ethanol model system would consider other key properties such as RVP, distillation, and V/L. A good ethanol model system would allow a refinery to achieve method repeatability level giveaway for all their constrained parameters and maximize the benefit from production cost management.
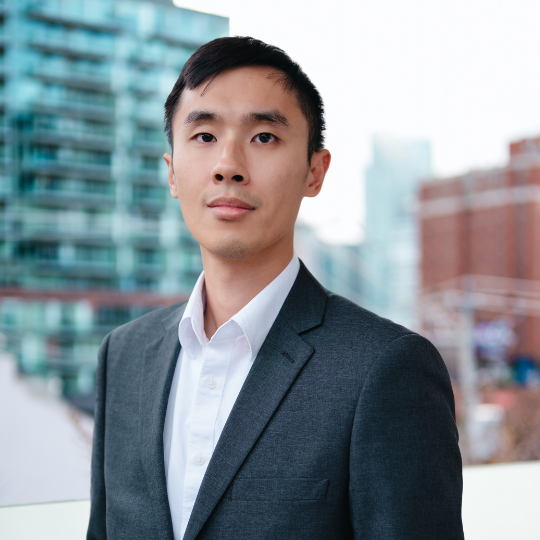
This article was written by KAI Y. WAN, an Associate Principal at Trindent Consulting. Dr. Wan has collaborated closely with multiple business partners in the energy sector across North America and Asia-Pacific, including some of the world’s largest refineries, and has delivered > $300 MM in financial improvements, with typical project ROIs at 500%–1,500% during the first year after implementation.
How Does Butane Affect Gasoline Blending?
Butane is one of the most important components in gasoline blending and arguably one that could provide the most economic benefit to the bottom line of more and more skinny refinery margins. Butane has a high octane and high RVP which makes it the ideal component to improve the quality of gasoline blends, especially in Winter months. Along with its properties, it has a relatively low cost compared with other components making it the go-to ingredient when blending gasoline. Moreover, it could help companies to reduce the product quality giveaway, i.e. the difference between the specification and the actual product properties. It is estimated that each barrel of butane added to the gasoline blend represents an uplift of $40-50 of the final product.
Factors Influencing Butane Utilization
The management of butane is as important as the product itself considering the relatively large amount of product that is required during blending. To improve how well the butane is utilized, the following factors should be considered:
- Inventory capacity
- Sourcing: Internal production vs. external supply
- Product monitoring
The goal is to have enough butane available when blending in order to optimize the gasoline recipe, minimize giveaway and improve margins.
Inventory capacity: Consider doing a mass balance of butane not only for each blend but for an entire season (mainly Winter) to understand the total amount that will be required. It is recommended to include all the available tanks (accumulation), estimated gasoline production and butane percentage (out) and product sourcing (in). For perspective, butane represents about 10% of the total gasoline volume in wintertime, which is 4-5 times more than in summer.
Sourcing: After the total requirement of butane is determined, an important question has to be asked regarding its source: Is the refinery able to produce the total amount needed? Or does an external supplier need to be involved? If so, how often can you get the product? How soon in advance does the request need to be placed? How feasible is it to have an additional volume? How is the quality of the product and how to monitor it? Planning for the butane sourcing is recommended prior to the season to avoid last-minute pitfalls and secure steady availability through the season.
Product monitoring: This is one of the most critical factors to consider when managing butane – to be able to know the product location, quantity and quality at any given time. The information should be transparent and encompass all the stakeholders including butane storage levels, requirements for blending and other processes, internal movement of product, etc. so that decisions can be made promptly without bottlenecks. Data visualization tools are very important in order to convey information in the most efficient way possible. It is recommended to generate automated data without any additional effort.
Once the analysis is done all stakeholders must come up with a plan to address the weak points, generate solutions, and implement and track them. They can use this analysis to evaluate the outcomes for future seasons or expand to other processes or locations as needed. A combination of technical and managerial expertise is fundamental for excellent butane management in order to understand common problems, physical limitations, product specifications/components properties, and data manipulation. This further helps in engaging with the multi-function teams at different levels, motivating and coaching employees, and providing tools to effectively track results.
Maximizing Benefits through Advanced Process Control (APC) in Gasoline Blending
Introduction:
Advanced process control (APC) plays a crucial role in real-time analysis and recipe control for optimizing gasoline blending operations. However, to harness the full potential of these systems, users must be aware of key considerations. This article will explore three important caveats when implementing APC in gasoline blending: configuring the objective function, ensuring accurate parameters and constraints, and establishing a robust performance review process. By addressing these aspects, refineries can unlock the benefits of precise process control, automation, and financial advantages while adapting to lean operational environments.
Table of content:
Configuring the Objective Function
Parameters and Constraints
Performance Review Process
Benefits of a Well-Configured APC System
Conclusion
Configuring the Objective Function:
To achieve optimal results, configuring the APC system’s objective function is essential. Refineries must customize the solution to align with their specific refinery posture and economic goals. Often, default settings from initial installation are utilized without considering individual circumstances. Refineries should assess and update these settings regularly to maximize performance and value delivery.
Parameters and Constraints:
The accuracy and timeliness of data feeding into the APC system are critical for effective gasoline blending. Refineries must ensure that data sources are up-to-date, reflecting daily operations and incorporating the latest lab data. Careful attention should be given to the calibration and accuracy of the data. Additionally, refining the constraints is vital to strike the right balance. Overly flexible constraints can lead to excessive fluctuations during adjustments, while overly tight constraints may hinder the system’s ability to provide optimized solutions.
Performance Review Process:
Regular performance reviews are essential to ensure that the APC system remains up-to-date and continuously improves. Refineries should establish a robust review process to assess the system’s configuration and identify additional optimization opportunities. By periodically evaluating system performance and exploring new features, refineries can enhance their operational efficiency, identify potential areas for improvement, and capitalize on emerging technologies.
Benefits of a Well-Configured APC System:
A well-configured APC system in gasoline blending brings numerous benefits. It enables precise process control, ensuring the production of optimal-quality gasoline within specifications. The high level of automation reduces manual intervention and empowers process control engineers and operators. In lean operational environments, a well-configured APC system can generate significant financial benefits, potentially amounting to tens of millions of dollars annually.
Conclusion:
Maximizing the benefits of APC in gasoline blending requires careful attention to key considerations. Configuring the objective function to align with refinery goals, ensuring accurate parameters and constraints, and implementing a robust performance review process are crucial steps. By addressing these caveats, refineries can achieve precise process control, automation, and substantial financial advantages in an increasingly lean operational landscape.
Hydrocarbon value chain optimization: Non-CAPEX opportunities to improve gross margins for the downstream sector—Part I
Kai. Y. WAN, Trindent Consulting, Toronto, Canada
The oil and gas industry comprises some of the most complicated manufacturing processes, involving mining, transportation, refining, distribution and retail.
Refining operations require a deep understanding of various refining techniques, including distillation, cracking and hydrotreating, among others. Implementing advanced technologies and optimizing process efficiencies are crucial steps toward achieving higher yields and reducing operational costs.
Meanwhile, the refining industry is inherently susceptible to market fluctuations, including raw material cost volatility, demand fluctuation due to global events and competition from renewable energy. To succeed in this dynamic environment, refiners must adopt cost-efficient operations that allow for quick adjustments in production levels and product portfolios.
A critical step in this process, collaboration with upstream and downstream partners is essential for refining success. Establishing robust relationships with crude suppliers, transportation providers and distributors enables smoother operations and increased negotiating power. Additionally, supply chain optimization principles, including efficient logistics and inventory management, can lead to reduced costs and improve overall profitability.
Part 1 of this article will outline a series of opportunities that oil and gas operators can consider immediately without the need for any capital expenditures (CAPEX) or software upgrades. These opportunities typically bring in strong cash flow performance within months and can improve gross margins significantly within a brief period of time.
CRUDE SELECTION: ENHANCING QUALITY MONITORING AND OPTIMIZING VALUE
Crude assay quality. Characteristics such as API gravity, sulfur content, distillation characteristics, Reid vapor pressure (RVP), total acid number (TAN), metal content, viscosity, asphaltene and resin content, pour point and cloud point all play pivotal roles in determining how a crude integrates within a refinery.
As crude oils traverse pipelines, their characteristics may undergo alterations. Consequently, comprehensive analyses at both the wellhead and refinery gate are essential. The information gathered serves as critical input for refinery operations, ensuring that refining units are optimally tuned to handle the specific qualities of the incoming crude.
Refineries that prioritize accurate crude assay quality assessments at both ends of the transportation journey can potentially gain tens of cents per barrel. These gains reflect enhanced operational efficiency and the prevention of potential processing challenges and equipment issues.
For example, a U.S. refinery situated at the end of the pipeline observed consistent crude assay performance at the refinery gate despite purchasing different types of crudes. The long distance between the injection point and the receiving point, coupled with breakout tankage on the route, allowed the crude flowing through the pipeline to mix. The refinery successfully adapted its strategy by using advanced data analytics to discount the impact of purchased crude at the injection point, enabling it to focus more on the real-time price optimization of the raw materials.
Without the proper crude assay analysis at the gate, a small refinery located near the U.S. Gulf Coast observed significant inconsistency in its linear programming (LP) model prediction when compared against the actual refinery yield profile. This was especially evident for its fluid catalytic cracker unit (FCCU). After a thorough investigation, it was observed that the crude purchased had changed its characteristics significantly during transportation and tank storage phases across the U.S. pipeline system. Using the crude assay profile information collected at the wellhead resulted in overestimating the distillation and sulfur content for the actual crude received at the refinery, which led to an inaccurate LP prediction of the chemical process. By adapting to a refinery gate crude assay program, this refiner was able to quickly adjust the crude assay input into the LP and create a more optimized plan for operation.
Crude sensitivity analysis. A key tool in achieving optimal raw material cost control is the crude sensitivity analysis, commonly known as the crude curve. The crude curve provides a detailed breakdown of the sensitivity of various crudes to changes in market prices. This practice guides supply chain teams, driving the process for how to strategically switch crude types in response to changing market dynamics and ultimately preventing costly procurement oversight. The crude curve helps crude planners to understand how different grades of crude value to the asset respond to shifts in price, allowing for precise decision-making in the procurement process.
This tactical approach has the potential to generate significant savings in the range of cents per barrel. Armed with the insights from the crude curve, supply chain teams are equipped to make informed decisions in real time. This includes determining the optimal mix of crude oils to refine, considering price differentials, availability and processing capabilities. By aligning procurement strategies with the ever-fluctuating market, refiners can seize opportunities and mitigate risks.
For example, FIG. 1 shows a simple type of crude sensitivity analysis for a refinery. Per the scenario illustrated, the crude planner can decide to switch crude purchases between Type A and Type B based on the current market price.
FIG. 1. Example of a simple crude sensitivity analysis.
Usually, the crude procurement plan for each refining asset is announced before the trading cycle. If this plan is not adjusted in real time—frequently applying market price fluctuations—market dynamics may put the original crude procurement plan at a disadvantage. By simultaneously conducting the crude sensitivity analysis when the crude procurement plan is published, crude planning teams can use a data-driven approach to respond to market price changes and optimize the cost structure of the refinery in real time during the trading cycle.
Without this tool, refiners may inadvertently lock in contracts for crude oil purchases that become uneconomical due to unexpected market shifts. The crude curve acts as a safeguard, providing a clear roadmap for adjusting procurement strategies to align with prevailing market conditions.
Working capital integration with planning. Not all crude source contracts are created equally. They vary in payment terms, credit provisions and contractual obligations. Refiners that take the time to scrutinize these contracts and align them to their operational realities can make precise decisions for when and how to allocate capital. This strategic approach ensures that financial resources are deployed efficiently, minimizing idle capital and maximizing returns.
FIG. 2. Working capital consideration during crude selection.
As illustrated in FIG. 2, a refinery with access to maritime crude delivery is presented with two different crude options. Option A may be a relatively cheaper option, but this crude would take about 30 d to be delivered to the refinery. Option B may be a relatively more expensive option but, due to its close proximity, the raw material can be delivered to the refinery within 3 d after an order is placed. Both suppliers have agreed to a Net 30 payment term, and the refinery has an average of Net 7 payment terms on refined products for all of its customers. The average crude on-hand time can be estimated at about 4 d before the crude is processed at the refinery. When comparing the two possibilities, Option A presents the refinery with a maximum financial exposure at the crude price per barrel. In contrast, Option B, due to its close proximity, offers the refinery a zero financial exposure as the payment of the refined product typically occurs before the due date for the crude purchase. An internal cost of capital of 10% means a price difference of $0.91/bbl may render no difference for both crudes, assuming an equal product value of $111/bbl. A simplified calculation to explain this concept is shown in
TABLE 1—the actual operation of factoring working capital during crude selection is much more complicated.
The financial impact of a refiner’s ability to be highly adept at working capital management is substantial. Refiners that fine-tune their capital allocation strategies based on varying crude source contracts can realize gains in the range of cents per barrel. Over time, these seemingly incremental gains accumulate into significant boosts to the bottom line.
PLANNING AND FORECASTING: STRATEGIC POSITIONING FOR SUCCESS.
Unconstrained LP analysis. Refiners should consistently evaluate sales constraints in their models for high-value products. Marketing efforts aimed at promoting and prioritizing the high-value products can yield substantial returns for refineries. One potential profit-driving opportunity is the distribution between premium gasoline vs. regular gasoline and jet vs. diesel, for example. It is worth noting that marketing initiatives should align seamlessly with the refinery’s operational capabilities and market demands.
This initiative can typically be identified when performing sensitivity analysis compared to the base LP case by opening product demand constraints one-by-one, and eventually removing all of them. This will enable the LP to fine-tune operational parameters, such as crude slate, processing capacities, product yields and production schedules. Such an analysis will define the business development direction to debottleneck current demand constraints, allowing the company to increase production throughput, as well as increase the ratio of the higher value product.
A case study completed for an integrated energy company by the author’s company indicated that this operator could focus on securing a contract to sell jet fuel to a nearby major airport. This carried a potential financial benefit of > $1/bbl. Note: The final opportunity was reduced by logistic costs and CAPEX.
The fiscal impact of this strategic marketing initiative is substantial. Refiners that prioritize high-value products can realize returns ranging from tens of cents to dollars per barrel. These gains, when extrapolated over time, translate into significant enhancements to the refinery’s bottom line.
Unit constraint optimization. Unit constraints dictate the operational limits of various refining processes. Regularly assessing and potentially challenging these constraints are essential practices, opening the door to uncovering inefficiencies, streamlining operations and ultimately boosting profitability.
For instance, the author’s company completed a case study for a refinery demonstrating that revising one unit constraint would subsequently generate a financial benefit of $0.10/bbl. Without regularly reviewing the unit constraints and performing the required LP optimization study, it is difficult for a refiner to prioritize among different opportunities and focus on the high profit drivers.
The financial impact of this strategic practice is substantial. Refineries that diligently assess and challenge unit constraints can potentially gain in the range of tens of cents per barrel.
PEOPLE: HIGH-PERFORMING TEAMS WITH CLEAR ROLES ANDRESPONSIBILITIES.
While the preceding sections have focused heavily on the technical aspects for how oil and gas operators can yield significant financial benefits without substantial capital investment, an often-underestimated factor is the human element in these processes. A high-performing team with clearly delegated authority and responsibilities is integral to a robust continuous improvement process. A few high-level concepts are discussed below.
Throughout engagements with clients, the author’s company has frequently encountered undefined roles and responsibilities for cross-functional areas like planning or blending, resulting in internal friction and rework. While opportunities can be overlooked without clear ownership, well-established accountability tends to drive individuals to claim ownership of their processes and enhance the performance of their designated areas.
An area where inefficiencies commonly arise is in the effectiveness of management meetings. The purpose of these meetings should be well-defined in advance, action items must be documented and regularly followed to support holding key stakeholders engaged and accountable for sustainable change.
Meetings have been observed that cover the “what/where/when” but neglect addressing the “how/why” questions, hindering continuous learning, skill development and improvement.
Takeaway. In a rapidly evolving industry landscape, the implementation of the above-mentioned refining strategies can significantly enhance refinery profitability and position them for sustained growth. By leveraging these opportunities, refiners can navigate market challenges, adapt to changing conditions and secure their position as industry leaders in the ever-evolving world of crude oil refining.
KAI Y. WAN is an Associate Principal at Trindent Consulting. Dr. Wan has collaborated closely with multiple business partners in the energy sector across North America and Asia-Pacific, including some of the world’s largest refineries, and has delivered > $300 MM in financial improvements, with typical project ROIs at 500%–1,500% during the first year after implementation.
Pride Month 2024: Supporting 2SLGBTQI+ Artists
Celebrating Pride Month at Trindent
The history of Pride is rooted in resistance, resilience, and the pursuit of equality. It traces back to the early morning hours of June 28th, 1969, at the Stonewall Inn in New York City and is now a global movement celebrating how far we have come, and how far we still need to go.
Trindent is proud to be a supporter of the 2SLGBTQI+ community. 🏳️🌈
As part of our celebration of Pride, we’ve invited each one of our team members to pick a song by an 2SLGBTQI+ artist that inspires them. These selections have been compiled into a playlist we proudly call “Trindent’s Pride Month Playlist.”
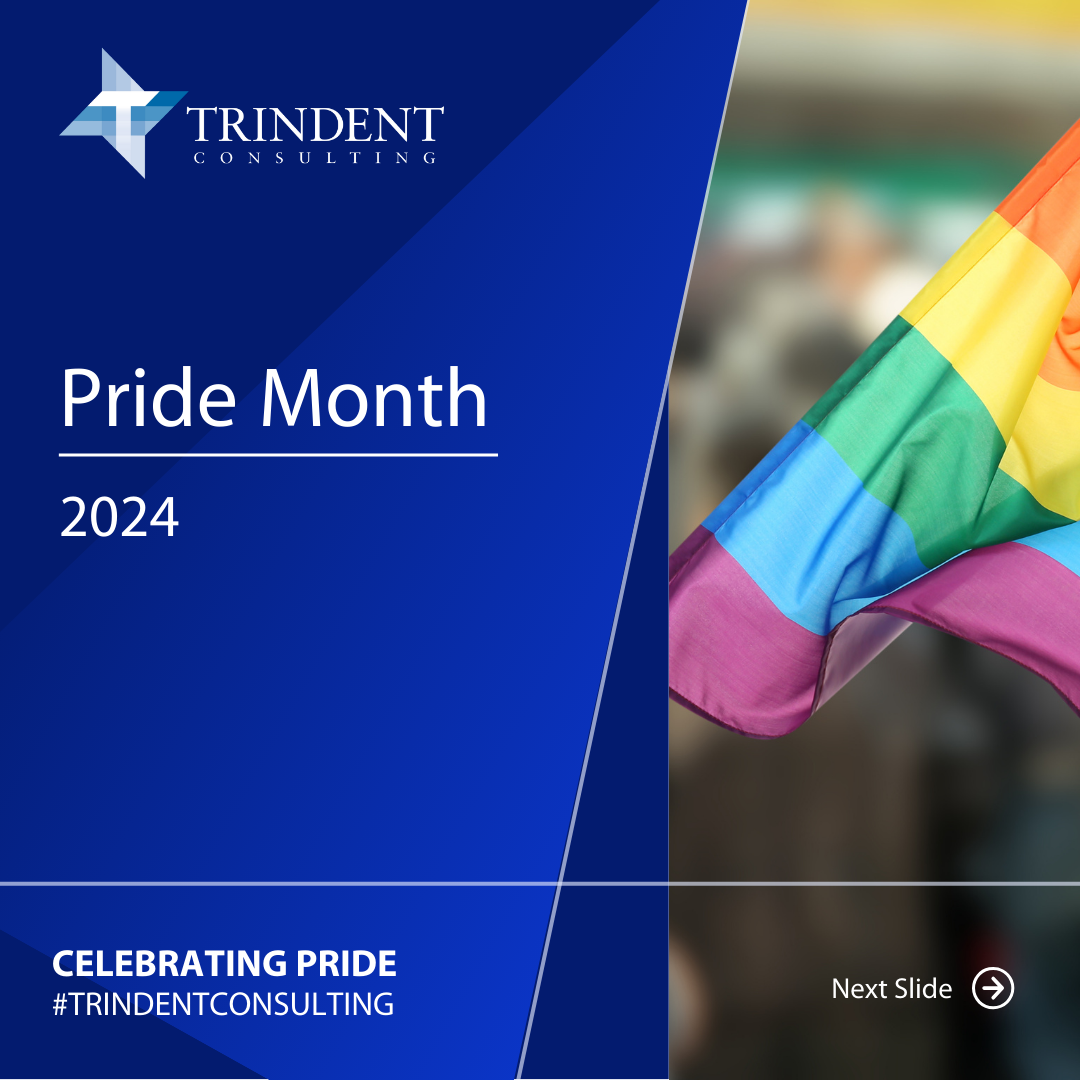
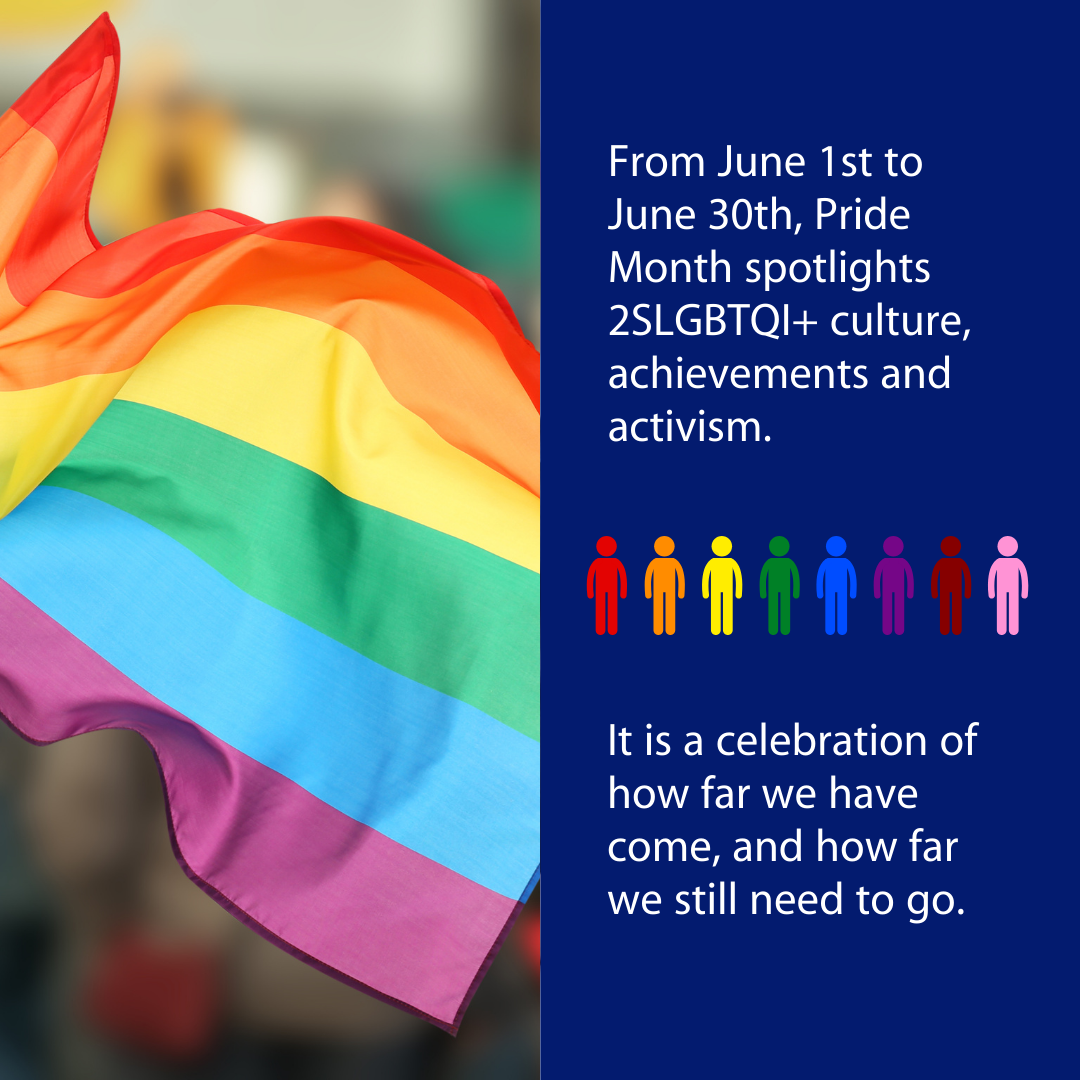
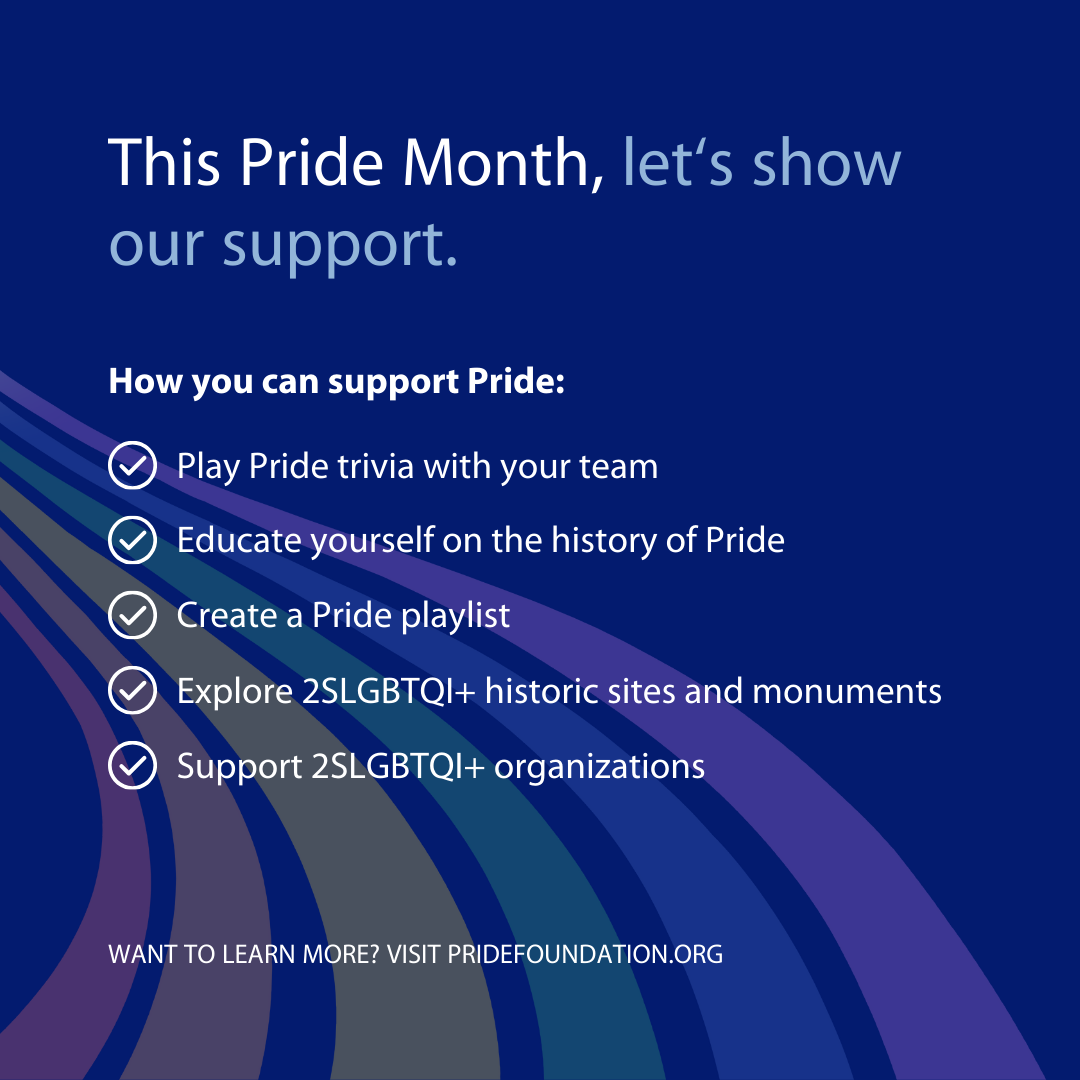
Be Proud. Be Unique. Be Yourself.
At Trindent Consulting, we are committed to diversity, inclusion and equal rights. This means that every team member is encouraged to be their authentic self at work and is empowered to express themselves freely, without any barriers.
Our inclusion and diversity strategy puts a strong focus on creating a comfortable and open work environment. We are committed to ensuring that every employee is allowed to excel regardless of their sexual orientation or gender identity.
Interested in joining our team? Visit our current openings page to learn more!
2024 International Womens Day
Today, on International Women’s Day, we take this moment to celebrate our esteemed women at Trindent Consulting and all the incredible women around the globe for their dedication, expertise, and passion!
At Trindent Consulting, we’re committed to empowering women in the workplace, fostering a culture of equality, diversity and inclusion.
We are always on the lookout for new talent, and we want to welcome more women to our team! Interested? Check out our Current Openings page!
Let’s continue to support, uplift, and empower one another. 💜💪
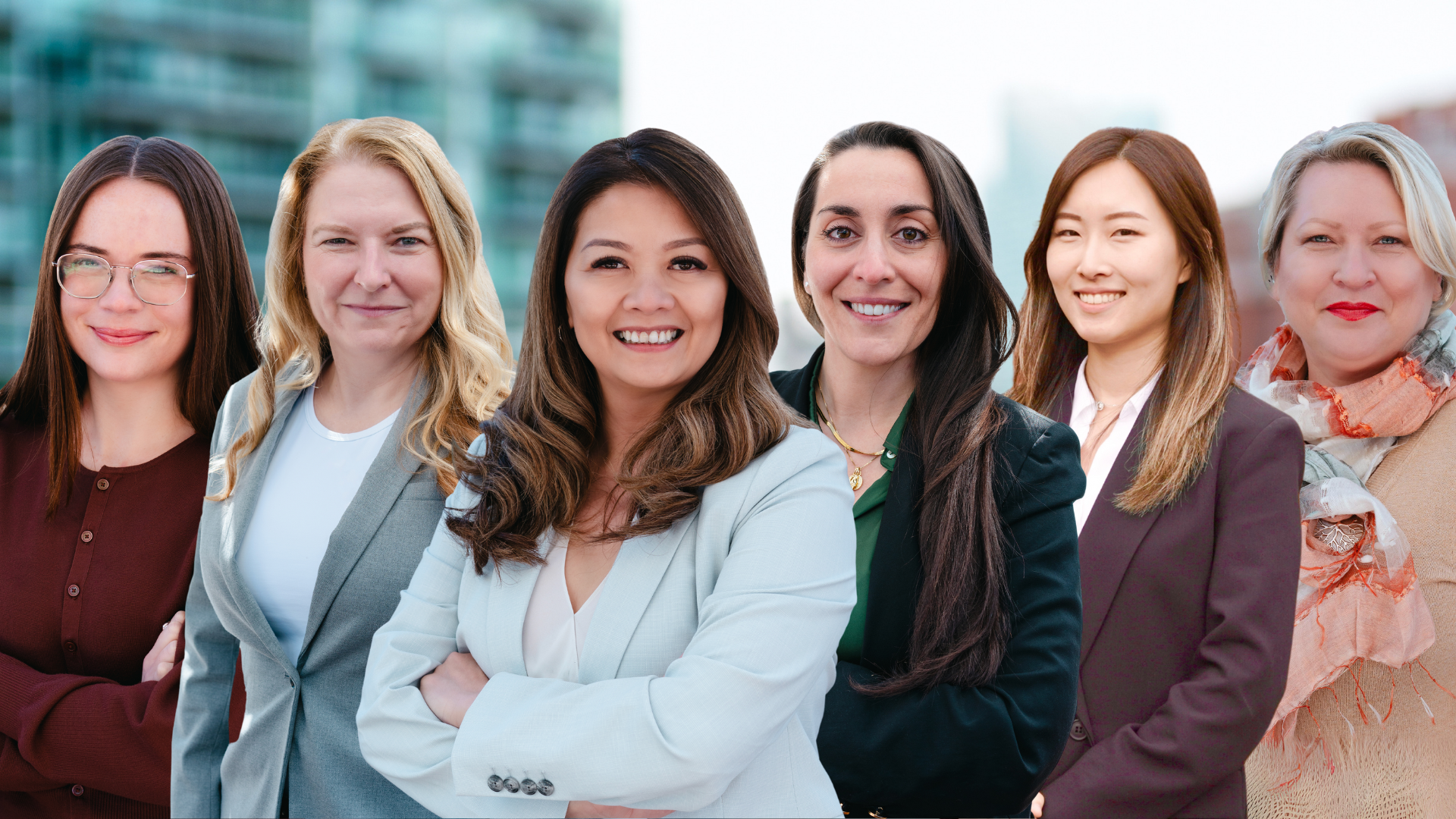